샌드위치형 레이돔의 전기적 성능개선 위한 성형압력 영향성 연구
A Study on Effects of the Cure Pressure for the Improvement of the Electrical Performance of the Sandwich Type Radome
Article information
Trans Abstract
Purpose:
This paper analyzes the phenomenon on the degradation of the electrical performance by the pressure in the manufacturing process of sandwich type radomes.
Methods:
This paper consists of two steps to analyze the relation between the electrical performance and the pressure. First, the thickness of the core of the flat panels which were fabricated with different pressure was measured with the microscope, and then the electrical performance of the flat panels was analyzed with simulation and experiment. Based on the results of the electrical performance and the measured thickness with respect to the flat panels, the relation between the electrical performance and the applied pressure in the manufacturing process was analyzed.
Results:
The simulated and measured results with respect to the flat panel shows that the high pressure results in the nonuniform thickness of the core, which is applied to the radome fabrication. As a result, the degradation of the electrical performance occurs because the unintended scattered field is generated as the electromagnetic wave transmits (or impinges upon) the radome. Furthermore, we observed that the electrical performance of both the flat panel and the radome got worse as the high pressure was applied.
Conclusion:
Through simulation and experiment, therefore, it is demonstrated that for the high pressure in the manufacturing process the nonuniform thickness of the core increases and results in the degradation of the electrical performance of the radome.
1. 서 론
레이돔(radome)은 지상장비나 항공기 및 미사일 등에 탑재된 안테나를 비, 우박 그리고 먼지 등과 같은 외부 환경 요인으로부터 보호하기 위해 사용되는 구조물이다. 일반적으로 레이돔은 안테나를 둘러싸는 주변 위치에 존재하기 때문에 전력 투과율(transmission efficiency), 보어사이트 오차(boresight error), 안테나의 빔폭(beam width), 패턴 리플(pattern ripple), Power Handling 등과 같은 전기적 성능(electrical performance)이 저하되는 현상이 발생한다. 따라서 전기적 성능의 저하를 최소화 하는 것이 레이돔 설계의 핵심이 된다. 레이돔의 전기적 성능에 영향을 주는 인자로는 내․외부 곡면 기울기, 두께 등의 형상 설계치, 재료의 유전율 그리고 제조과정의 공정변수 등을 들 수 있다. 기존의 연구논문들은 레이돔의 전기적 성능 해석과 소재의 유전율에 대한 연구 사례는 많이 있으나, 레이돔의 제조과정 중 사용 소재의 재단이나 성형 등에서 발생할 수 있는 공정변수에 따른 전기적 성능에 대한 분석과 관련된 연구는 드물었다.
레이돔 제작 전문업체인 한국화이바는 개발 이후 양산과정에서 발생한 레이돔 관련 품질사안에 대한 개선방안을 검토한 결과, 레이돔의 전기적 성능개선에 있어서 제조과정 중 영향을 줄 수 있는 중요한 공정변수로서 크게 두 가지로 구분되었다. 첫 번째는 원하는 두께를 얻기 위하여 소재를 재단하는 과정에서 발생하는 두께 공차(tolerance)로서 이는 레이돔 성능에 영향을 주는 직접적인 요인으로 전파 투과 시 원하지 않는 부분적인 전자기 반사와 산란이 발생하기 때문에 재단 시 공차를 작게 유지하는 것이 중요하다. 두 번째는 소재 적층 후 원하는 형상의 레이돔을 제작하기 위하여 성형공정이 요구되는데, 이 과정에서 과도한 성형압력은 레이돔 두께의 불균일을 초래하여 전기적 성능을 저하시키는 원인이 된다. 따라서 의도한 전기적 성능을 얻기 위해서는 각 소재의 두께 공차 관리와 성형공정 시 최적의 압력값을 선정하는 것이 중요하였다.
본 논문에서는 레이돔의 경우 제조공정 중 소재 재단공정과 성형 공정변수인 온도나 시간의 측면보다는 압력의 변화가 전기적 성능에 미치는 관계를 분석하는 것을 목적으로 하였다. 그 이유는 시험편 제작시 노멕스 허니콤코어는 소재특성상 강도가 상당히 낮아 가공설비 여건상 일정한 두께로 가공이 상당히 힘들기에 전기적 성능에 미치는 영향성 요인으로는 배제하였다.
따라서 제조공정 중 성형압력에 따른 레이돔의 전기적 성능을 분석하기 위하여 다음과 같은 절차로 진행하였다. 우선 항공기에 탑재된 RF 송수신 시스템을 보호하는 레이돔에 사용되는 소재인 노멕스 허니콤(nomex honeycomb), 쿼츠(quartz)와 고분자수지인 에폭시를 이용하여 레이돔의 제조공정과 동일한 방법으로 평판 형태의 시험편으로 제작하였다. 다음으로 제작된 각 시험편의 중앙부와 측면부에서 절단하여 채취한 시편의 단면을 광학현미경 조사를 통해 측정된 코어 층의 두께 치수를 바탕으로 시뮬레이션 및 실험을 평판 시험편에 대한 성형압력에 의해 발생되는 두께 변화와 전기적 성능과의 상관관계를 분석하였다. 끝으로 실제 레이돔을 제작하여 성형압력에 의해 변화된 두께 변화와 전력 전달률과의 관계가 평판 시험편에 대한 결과와 유사한 경향을 나타내는지에 대해서 분석하였다.
본 논문의 구성은 다음과 같다. 2장에서는 레이돔 제작을 위한 공정 과정과 시험편 제작에 대하여 기술하고, 평판 시험편의 전력 투과율을 분석하기 위한 이론에 대하여 다루었다. 3장에서는 평판 시험편을 제작할 때 각각 적용된 성형압력 값에 따라 변화된 코어 층 두께를 측정하고 이를 바탕으로 예측모델을 이용하여 레이돔의 전력 투과율 분석하고, 평판 시험편 및 레이돔에 대한 전파성능시험을 통한 전력 투과율 결과를 상호 비교해 봄으로써의 성형압력과 전기적 성능과의 관계를 분석하였으며, 끝으로 4장에서는 본 논문의 결론을 기술하였다.
2. 레이돔 제조와 전기적 성능 예측모델
2.1 레이돔 제조공정과 시험편 제조
본 장에서는 레이돔의 제조과정에서의 적용소재와 공정특성 그리고 시험편 제작에 대해 살펴보고, 레이돔 성능에 미치는 영향을 예측하기 위한 방법에 대해서 기술한다.
본 연구의 대상은 항공기에 탑재되는 ASPJ(Airborne Self Protection Jammer)용 레이돔으로서 Figure 1과 같은 A 샌드위치(sandwich) 유형의 구조물이며, 사용되는 소재로는 심부 소재는 노멕스 허니콤이며, 외피 소재는 쿼츠와 고분자수지인 에폭시로 구성된다. 이러한 유형은 현대 항공기용 구조물의 성형이나 제작에 있어 널리 적용되고 있는 방식으로서 노멕스나 알루미늄 허니콤을 심부(core) 소재로 하고, 탄소섬유와 에폭시 등의 복합재료를 외피(skin) 소재로 사용하기 때문에 재료의 지나친 무게증가 없이 높은 강도와 강성 확보가 가능한 장점을 가지고 있다.
레이돔의 제조공정은 Figure 2와 같이 먼저 소재들을 레이돔의 외부 형상 틀에 맞게 재단하여 레이돔 형틀에 적층을 한 다음 성형 챔버(chamber) 내에서 원하는 형상을 위해 전방부와 후방부를 각각 설정된 압력, 온도 그리고 시간하의 오토클레이브(autoclave) 경화 공정에 의하여 제조된다.
얇은 외피를 지닌 샌드위치 유형의 구조물을 오토클레이브 방식으로 성형을 할 경우 오토클레이브 압력에 노출된 면에서는 성형압력에 의해 외피 소재가 심부 소재인 허니콤 셸(cell) 내부로 밀려들어가는 텔레그래핑(telegraphing) 현상이 발생한다. 이 현상으로 인해 심부 소재의 셸과 접촉된 외피 소재와의 간격이 불균일해져 레이돔의 두께 불균일을 초래하여 전자파가 투과할 때 원하지 않는 산란현상을 발생시키기 때문에 전기적 성능을 저하시키는 원인이 된다.
레이돔 제작시 성형압력에 의해 발생한 현상이 전기적 성능에 미치는 영향을 분석하기 위하여 다음과 같은 방법을 적용하였다. 우선 샌드위치 구조의 평판 시험편을 레이돔 제조공정과 동일한 방법으로 Table 1과 같이 제작하였으며, 그 구조와 형상은 Figure 3과 같다. 제작된 평면 시험편의 중앙부와 측면부를 절단하여 1㎝ 간격으로 단면부를 광학현미경을 통하여 측정한 허니콤 코어층의 평균 두께 결과를 반영하여 다음 장의 이론을 이용하여 전력 투과율을 계산하였다.
2.2 전기적 성능 예측모델
평판 시험편의 절단된 단면부에서 측정한 성형 후 심부 소재의 두께 결과값을 이용하여 성형압력과 전기적 성능과의 관계 분석은 “Analysis of radome-enclosed antennas” 문헌에 제시된 샌드위치형 레이돔의 전파투과 해석을 위한 계산식을 적용하였으며, 계산식은 세부 내용은 다음과 같다.
Figure 4는 N개의 유전체 층(dielectric layer)으로 구성된 평면 샌드위치(sandwich) 구조를 나타낸 것이다. 본 구조에 대한 전력 투과계수(transmission coefficient)는 전자기 경계조건(boundary condition)을 이용하여 계산할 수 있다. Figure 4와 같이 오른쪽으로 진행하는 파를 C로 정의하고 왼쪽으로 진행하는 파를 B라고 하면 입사파와 반사파 그리고 투과파의 관계식은 식 (1)과 같다.
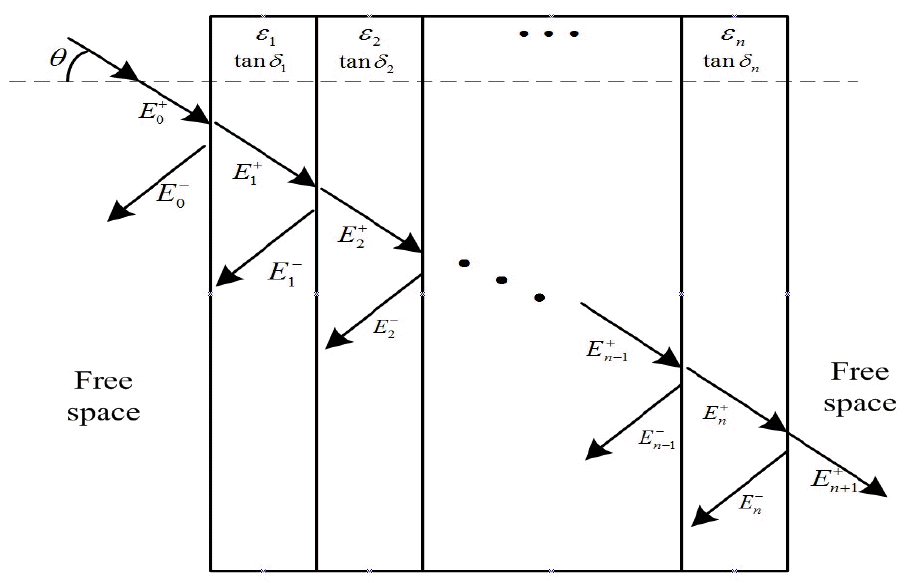
Transmission and reflection of electromagnetic wave in sandwich plane consisting of N number of dielectric layers
식 (1)에서 ti는 i번째 유전체 층의 두께를 나타내며, Ri와 Ti는 각각 i번째 유전체 층에 해당하는 프레넬 (Fresnel) 반사계수(reflection coefficient)와 투과계수(transmission coefficient)를 의미한다. 또한 γi는 i번째 유 전체 층에서의 전파 진행 상수이다. 전파 진행 상수(propagation constant)는
여기서 각 유전체 층의 파동 임피던스는 평면의 법선벡터와 입사진행 방향이 이루면 평면에 대해 수직 편파(perpendicular polarization)와 수평편파(parallel polarization)로 나누어 표현된다. 수직 및 수평 편파에 대한 파동 임피던스는 각각 식 (3), 식 (4)와 같이 표현할 수 있다.
식 (1)의 행렬 곱 계산을 수행하면 결과는 식 (5)와 같이 표현할 수 있다.
N+1영역에서는 좌측으로 진행하는 파(반사파)가 없으므로 BN+1는 0이 된다. 최종적으로 N개의 유전체층으로 구성된 평면의 수직, 수평편파에 해당하는 투과계수는 식(6)과 같이 계산할 수 있다.
3. 해석 및 시험 결과
3.1 전기적 성능의 이론적 예측
본 장에서는 레이돔 성형 시 적용된 압력 값이 전기적 성능에 미치는 영향에 대해 이론적 분석과 시험편을 이용한 성능시험의 결과 분석에 대해서 다룬다. 전기적 성능인 전력 투과율의 이론적 분석을 위해 필요한 특성으로는 시험편 제작에 사용된 소재의 유전 특성값과 두께, 사용 주파수, 전파의 입사각도 그리고 제조공정 후의 형상치수 등이 있다. 본 연구에서는 복합소재의 유전 특성값과 두께로는 외피 소재인 쿼츠/에폭시의 비유전율은 3.2, 로스 탄젠트는 0.1, 두께는 각각 0.4mm, 0.6mm 이며, 심부 소재인 노멕스 허니콤의 비유전율은 1.1, 로스 탄젠트는 0.003, 두께는 2mm 이다. 그리고 전력 투과효율 분석을 위해서 코어의 두께는 평판 시험편의 평균 두께를 적용하였으며, 안테나의 편파특성은 수직 및 수평 선형편파이며, 전파의 입사각도는 0° 이고, 주파수는 0.0 ~ 00.0GHz내에서 0.1GHz 단위로 계산하여 평균값을 취하였다.
레이돔 제조시 성형압력은 사용 소재와 크기 그리고 구조형태에 따라 설정값이 각기 다른 바, 본 연구대상인 레이돔은 허니콤코어와 에폭시 프리프레그(prefreg)로 구성된 샌드위치형 스킨으로 제작된 국내 군사용 무인항공기용 구조물과 유사하기에 그 작업표준(10~30psi(0.7~2.1kg/cm2))과 제조업체 작업표준(2.8kg/cm2)을 참조로 하여 1.5kg/cm2, 2.0kg/cm2, 2.8kg/cm2의 3단계의 성형압력으로 구분하여 평판 시험편을 제작하였다. 또한 시험편의 심부 소재의 두께 공차는 ±0.1mm 보다 작게 유지시킨 상태로 가공하고, 성형한 후 시험편의 중앙부와 측면 끝단부를 절단하여 1㎝ 간격으로 단면을 광학현미경(X100 배율)을 이용하여 성형 후 변화된 코어층의 두께를 Figure 5와 같이 측정하였다. 그리고 성형압력에 따른 코어층의 평균 두께 변화를 Figure 6에 나타내었다.
성형압력이 1.5kg/cm2 일 때 평균 두께는 1.87mm 이며, 편차는 0.07mm 이고, 성형압력이 2.0kg/cm2 일 때 평균 두께와 편차는 각각 1.73mm, 0.1mm 이며, 끝으로 성형압력이 2.8kg/cm2 일 때 평균 두께는 1.78mm 이며, 편차는 0.15mm 이다. 이 결과로부터 성형압력이 낮을수록 코어층의 두께 편차가 적게 나타남을 확인할 수 있었다.
다음은 제작된 평판 시험편의 전기적 성능을 이론적 계산에 의하여 분석하기 위해 2장에서 언급한 방법을 적용하여 전력 전달효율을 계산하였다. 그리고 평판 시험편에 대한 전력 전달율 시험은 Table 2에 언급된 시험기기를 사용하여 무반향 챔버(anechoic chamber) 내에서 Figure 7과 같이 송․수신 안테나간의 거리는 평판 시험편의 크기를 고려하여 0.7m로 하고, 표준 안테나는 주파수 범위 내에서 3종류의 안테나를 사용하였으며, 수직과 수평 편파 조건으로 하여 평판 시험편의 설치 전․후의 전파투과 성능을 측정한 결과값을 전달율(%)로 계산하였다. 시험편의 이론적 해석결과와 시험결과를 비교하기 위해 안테나의 편파조건별로 구분하여 Figure 8과 9에 나타내었다.
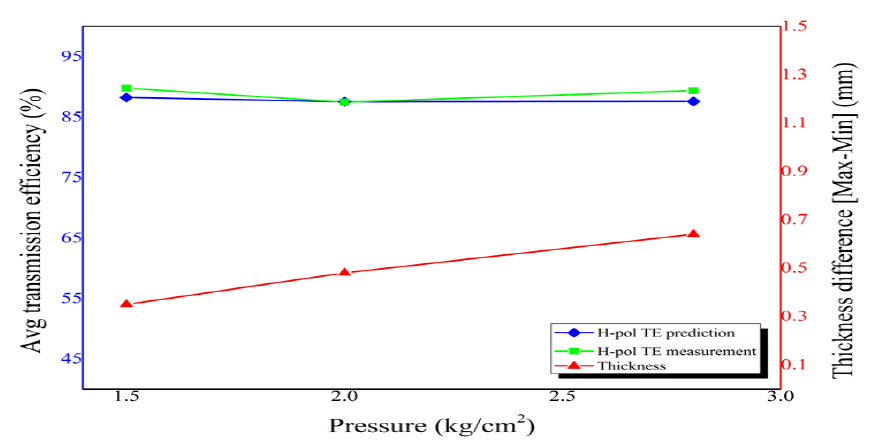
Average transmission efficiency of flat plate according to cure pressure in horizontal antenna polarization
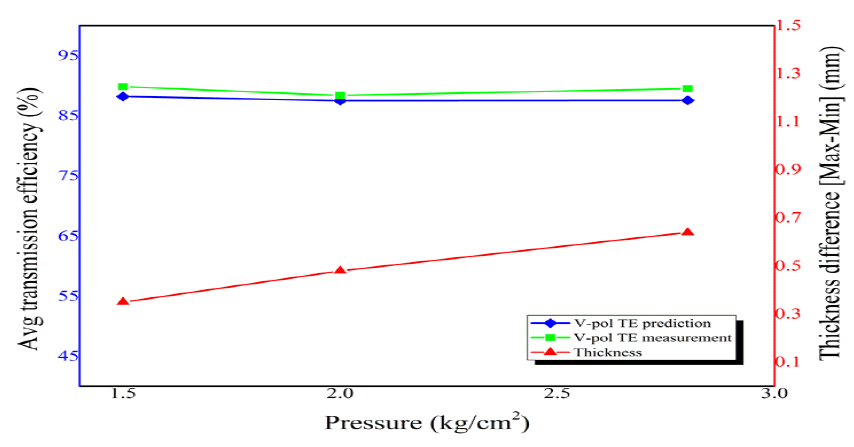
Average transmission efficiency of flat plate according to cure pressure in vertical antenna polarization
수평편파 조건에서의 전력 전달율 평균값은 Figure 8에서와 같이 이론적 해석결과는 성형압력이 1.5kg/cm2 일 때 88% 이고, 2.0kg/cm2 일 때는 87% 이며, 2.8kg/cm2 일 때는 87% 로 나타났으며, 시험편의 전력 전달율은 성형 압력이 1.5kg/cm2 일 때 90% 이고, 2.0kg/cm2 일 때는 88% 이며, 2.8kg/cm2 일 때는 89% 로서 레이돔 제조공정의 성형압력 값이 증가할수록 코어의 두께 변화가 크게 나타나 두께의 불균일 정도는 증가하였으나, 전기적 성능인 전력 전달율의 평균값은 이론적 해석이나 시험의 결과 모두 변화폭이 미미하게 감소하는 같은 경향임을 확인할 수 있었다. 또한 Figure 9와 같이 수직편파 조건에서도 동일한 결과로 나타났다.
이같이 전력 전달률의 평균값 경우는 성형압력에 따라 변화의 폭이 적게 나타났으나, Figure 10과 11에서와 같이 전력 전달율 최소값의 경우는 성형압력에 따라 변화의 폭이 크게 나타났는데, 이는 성형압력의 변화가 레이돔의 전기적 성능 중 전력 전달율 최소값에 미치는 영향이 더 크게 나타남을 알 수 있었다. 앞 장에서의 Figure 5와 6에서 보았듯이 성형압력이 낮을수록 코어층의 두께 변화가 적게 나타났으며, 이로 인해 외피 표면에 텔레그래핑 현상 발생이 감소되어 전력 전달율의 최소값이 상당히 개선되었다.
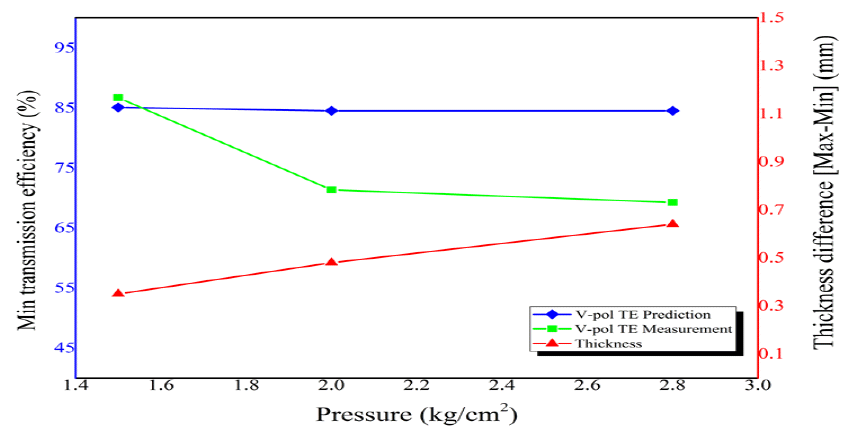
Min transmission efficiency of flat plate according to cure pressure in vertical antenna polarization
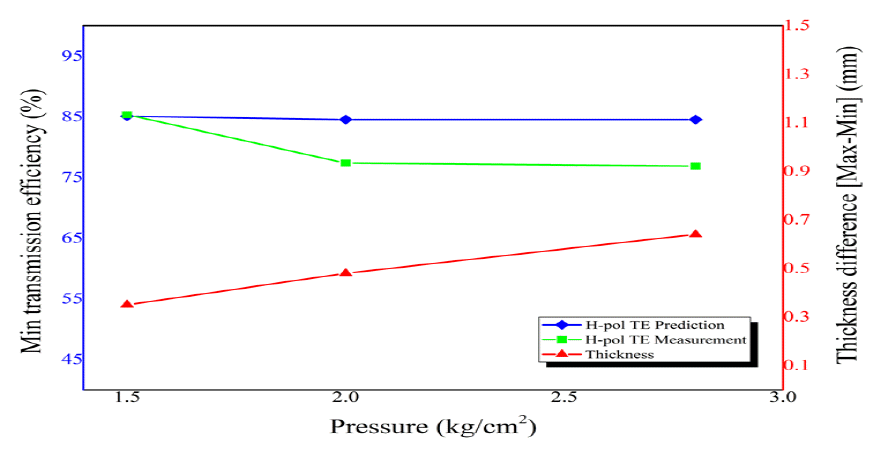
Min transmission efficiency of flat plate according to cure pressure in horizontal antenna polarization
이 성능예측 이론 모델을 이용하여 해석함에 있어 소재의 표면거칠기를 반영하기가 부적합하기에 전력 전달율의 최소값을 해석하기에는 충분하지 못하였다. 그 이유로는 제작된 평판 시험편의 표면거칠기를 앞 장에서 언급한 전기적 성능예측 이론모델을 이용하여 표현할 수 없는 제한조건이 존재하기 때문에 성능의 차이가 발생된 것으로 사료된다.
3.2 레이돔의 전기적 성능시험
제조과정의 공정변경 요소인 성형압력의 변화가 전기적 성능에 영향을 미침을 평판 시험편의 실험을 통해 보았듯이 항공기에 설치되는 실제 레이돔의 경우에서는 어떠한지를 알아보기 위하여 Figure 12와 같은 무반향 챔버 내에서 전기적 성능시험(전력전달률, 빔폭변화율)을 레이돔 국방규격의 시험방법에 따라 실시하였다. 시험방법으로는 레이돔의 방위각은 ±60° 이고, 안테나의 편파조건은 수직 편파로 하였으며, 운용 주파수 범위 내에서 0.1GHz 단위로 수신측 안테나에 레이돔을 장착하기 전과 후의 전력 전달율을 측정하여 계산한 결과의 평균값으로 나타내었다.
레이돔 완성품 시료 5개에 대해 수행한 전기적 성능시험 결과 중 수직편파 조건에서의 전력 전달률 최소값과 빔폭 변화율 결과만 나타내었다. Figure 13과 같이 성형압력이 1.5kg/cm2 일 때 전력투과율 최소값이 가장 높게 나타났으며, Figure 14와 같이 성형압력이 1.5kg/cm2 일 때 빔폭 변화율이 가장 낮게 나타났다. 이는 평판 시험편의 시험 결과를 통해서 확인 하였듯이 성형압력이 1.5kg/cm2 일 때가 코어층이나 스킨층의 두께 변화폭이 적었으며, 스킨 소재가 허니콤의 셸 내부로 밀려들어가는 텔레그래핑 현상 발생이 다른 성형압력에 비해 적음에 따라 스킨층의 두께가 균일하게 제작되어 전자파가 통과 시 산란현상 발생이 상대적으로 적었기 때문에 전기적 성능이 향상된 것으로 판단된다.
4. 결 론
레이돔에 대한 전기적 성능은 RF 송수신 시스템의 동작 주파수, 방사되는 전파의 편파 및 입사각, 레이돔 재질의 두께 등의 변수에 의하여 결정된다. 특히 이 중에서 레이돔 생산 시 고려해야 하는 사항으로는 코어 및 스킨 재질의 두께가 전자기적 성능 변화에 커다란 영향을 주는 요소가 된다.
본 논문은 레이돔의 제조과정에서 공정변수인 성형압력과 전기적 성능과의 관계에 대하여 다루었으며, 본 연구를 통하여 얻은 결론은 다음과 같다.
(1) 노멕스 허니콤, 에폭시 및 쿼츠 소재로 구성된 샌드위치형 구조의 레이돔과 동일한 제조방법에 따라 제작한 시험편의 단면 조사 결과, 성형압력이 1.5kg/cm2 일 때 코어층의 두께 변화가 가장 낮게 나타났다.
(2) 성형압력에 따른 코어층의 두께 변화를 바탕으로 한 이론적 해석과 평판 시험편에 대한 전기적 성능시험 결과, 모두 성형압력이 1.5kg/cm2 일 때가 가장 우수하였으며, 특히 전기적 성능 중 평균 전력 전달률 보다는 최소 전력 전달률에서 성형압력이 미치는 영향이 더 크게 나타났다.
(3) 성형압력을 달리하여 제작한 레이돔에서도 안테나의 편파특성과 무관하게 성형압력이 1.5kg/cm2 인 경우 전기적 성능이 가장 우수하였다.
위 실험결과로부터 성형압력이 낮을수록 전력 투과율이 향상됨을 알 수 있듯이 전자파가 레이돔을 투과할 때 허니콤코어와 스킨층간 두께의 불균일 정도가 적을수록 산란현상이 적게 발생하여 전기적 성능이 향상됨을 본 연구를 통해 확인할 수 있었다. 그리고 레이돔 제조의 최적 공정표준을 결정하기 위해서는 성형압력의 저하로 인해 레이돔 구조물의 강도측면에 미치는 영향성에 대해 추후 연구과제로서 수행할 필요가 있다고 사료된다.
본 연구에서 도출된 결과에 따른 공정기준은 현재 KF-16 항공기에 적용되고 있으며, 레이돔의 전기적 성능개선을 위해 제시된 공정변수 개선은 향후 다른 기종의 레이돔 제조 시 참고 사례가 될 것으로 기대된다.